Machine technology
New technologies for building industry
Finishing works have also been covered by the age of new technologies. The mechanized technology of application of dry building mixes invented in Europe has changed traditional operations in building and is becoming increasingly popular in Russia.
Mechanized surface plastering takes a huge burden from finishing workers, especially when it is necessary to perform a large scope of work on large-scale building facilities in a short period of time and assure high quality for surfaces.
All operations are performed on modern equipment by specially trained foremen in strict conformity with SNiP.
Mechanized technologies are used in poured-on-place flooring and wall, ceiling, and facade finishing. Plastering machines makes it possible to perform operations with a much higher quality, optimize labour expenditures, cut production time and, which is the most important result, cut the prime cost of square metre.
Adoption of mechanization has strengthened the superiority of mechanized labour over manual. The standard output of one plastering foreman is 6-28 m2 per shift and 130-170 m2 per month. At the same time, mechanized plastering yields four-to-five times as much, i.e., 25-32 and 550-750 m2, respectively.
Usually, one plastering machine is operated by a squad of 4-6 workers. The HQ plastering output of a squad of 5 plasterers is 2500-3000 m2 per month on average. Three professional mechanized squads of 15 plasteters are able to plaster a residential building of 10000 m2 in a month, whereas it will take the same number of workers four months to do it manually.
Thus plastering machines make it possible to significantly speed up finishing works and cut payroll expenses not only because fewer workers are involved but also due to the payment for actual output: usually, manual labour is 1.5-2 times as expensive as mechanized labour.
Mechanization makes it possible to produce ideally homogeneous and plastic mortars and mix them in amounts necessary for single-layer application per pass to the entire surface on large areas.
Modern, modified VOLMA dry mixes applied by the dotless mechanized method allow you to prepare a high-quality surface for final finishing more rapidly and at lower costs.
The main advantages of the machine method:
- lower prime cost
- more rapid course of operations
- lower manpower requirements
- reduced payroll expenditures
- high-quality surfaces.
VOLMA was one of the first companies in the building sector to establish the Department for Mechanized Technologies. Its professional sfaff know all intricacies of mechanized indoor and outdoor plastering. They know from A to Z all details and action of plastering equipment, have taken training courses in Europe, adapted the acquired knowledge, and confirmed their expertise on Russian building sites.
Their task is to provide practical assistance, training, and services to teams that use the mechanized method of plasterwork. A mobile unit of a technical expert and a mechanic is always ready to set off for your facility on a car with a set of equipment, plastering tools, and plastering machine repair tools and train your employees to apply VOLMA mixes by the mechanized, dotless method, perform start-up and commissioning of plastering outfits, and diagnose or repair your equipment.
Mechanized Operating Technique
In the initial phase prepare the equipment. Install the plastering machine in the plasterwork area, e.g., on one of the storeys of an apartment building. Assemble the machine as shown in the attached instruction manual. Connect to a Kaleta A-5 380 V 8.5 kWh power source and the water supply system; the input plastering machine pressure shall be at least 2.5 bars. However, a more reliable variant is to supply water to the machine from a 1 m3 container via a water station unit with a 0.8-1 kW hydraulic battery; as a result, continuous water supply will be assured, which affects the stability of the mortar mixture coming out of the mortar hose. Then install an auger-type pump and use silicone to screw the stator into the rotor, which will make it easier to start up the main gear motor. In addition, unscrew the stator from the rotor at the end of the working day and reassemble the node every morning during five days; thus you will extend the pump service life and assure the supply of a well-mixed mortar. Connect the air and the mortar hose to the mortar gun. Turn on the main switch, control switch, mortar feed switch, and water pump switch. Pour out the mix into the tank, set the required water feed level in the flow-metering flask, using the topping-up button, and adjust the mortar feed cone. Now the plastering machine is ready for use. It is easy to operate even for newcomers to building!
In the next phase prepare the working site and the bases for plastering; the surface shall be dry, durable, and have no mortar buildups; treat the metal parts with an anti-corrosion metal primer; the base shall not be frozen, and its minimal temperature shall be 50°C. Apply the primer using a sprayer or a nap roller. Pad strongly absorbing bases with VOLMA-Universal and poorly absorbing bases with VOLMA-Contact. Remove the construction waste from the working site.
In case of dotless plastering with VOLMA-Gips Active it is important to observe processing activities. Check the surface with a level before plastering, find the most bulging point and take it for zero, remember all the deviations along the wall, and apply the mortar to the base using a mortar gun perpendicularly at 200-250 mm from the surface with regard to the deviations; thus you will level the surface flat in advance. Apply the mortar from left to right and top-down in 70-100 mm wide strips. The strips shall overlap each other by 10 mm. Then do the primary mortar levelling top-down and from left and right with an h-shaped floater: the more frequently the floater deflects along the plane, the smoother will the surface be. This phase takes 10-20 minutes on a 10 m2 area. When the mortar loses mobility in 60-80 minutes upon application, trim the surface with a trapezoidal float at 80-90°, cut the pop-outs, fill the cavities with the trimmed mortar, and control the levelling and trimming procedures with a level. Then clean the bordering along the surface outline in 20-30 minutes, do the primary puttying, and fill the pot holes. Wet the surface with water in 20-30 minutes and rub it with a spongy patter; as a result, gypseous milk, that facilitates subsequent final puttying, will be released. Wet the surface with water and then glaze the surface by downward flicking with a façade putty knife at 80-90° within 24 hours but no sooner than 5-7 hours after the mix has tempered. Within 5-7 days the surface shall be ready for subsequent colouring, wallpapering, tile cladding, etc. The minimal layer for tile cladding shall be at least 10 mm in thickness. The surface plastering and dry-out time depends on the base absorbability, plaster layer thickness, and indoor temperature and humidity.
We offer a broad range of European-quality KALETA and PFT TM equipment. Their main advantages are reliability and a simple control system. Plastering and puttying machines are of significant help to finishers involved in plastering and puttying works. Such characteristics as portability, small size, and high performance make this equipment truly irreplaceable. The cost of this equipment in the secondary market is practically affected by its maintainability.
We also offer the specialized plastering tools by Olejnik. They have better practical reliability and performance as compared to their rivals and make possible surface finishing at a height ≤ 3 metres without additional building equipment, which leads to shorter finish work periods and reduced financial expenditures. A set of these tools duly used shall serve for one year. Their use significantly affects plastering output and quality of delivered surfaces.
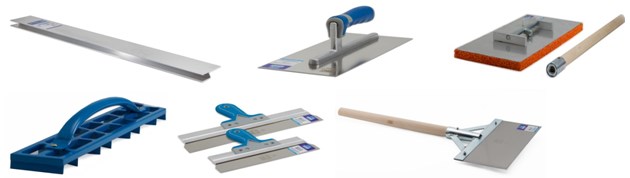
The multiple advantages of the mechanized technology lead to a natural conclusion that mechanized finishing works take far less effort than manual finishing works.